Inlet Guide Vanes for Centrifugal Air Compressors
Air Relief offers high-performance guide vanes that enhance the operation of centrifugal air compressors, saving energy and reducing maintenance expenses. Our products and services ensure your compressor systems operate at peak performance with long-term reliability.
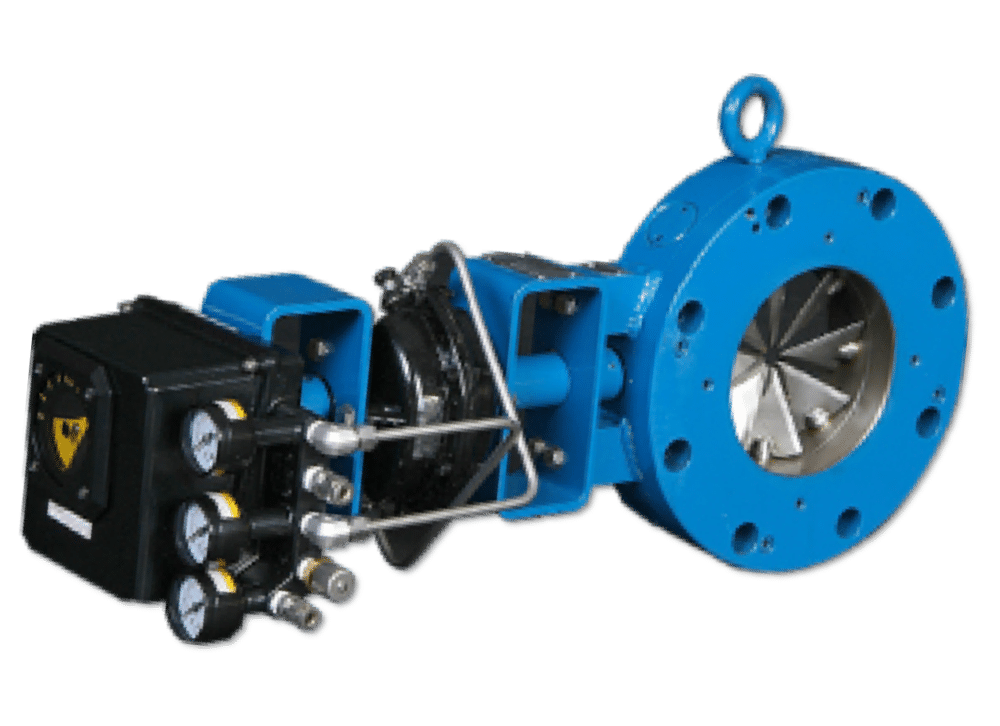
Benefits of Inlet Guide Vanes
- The internals are factory-lubed and sealed to prevent debris from entering the vanes
- Our stainless steel vanes eliminate corrosion
- It provides a tighter, more controlled system
- The thin-line style is only 2 inches wide
- We offer cost-effective solutions without sacrificing quality.
Cost Saving Benefits of Inlet Guide Vanes
- When throttled, inlet guide vanes reduce the horsepower required by pre-swirl air entering the first stage impeller, leading to increased energy savings (CFM per kW).
- Gear-driven valves offer smoother control compared to linkage-driven valves, reducing routine maintenance.
- In full-throttle mode, these vanes can reduce amperage consumption by 3 to 7% compared to butterfly valves.
- The return on investment (ROI) can be as short as one year, depending on your location and energy costs.
Recommended Maintenance
Our gear-synchronized guide vanes are designed for minimal upkeep. However, periodic maintenance is essential to ensure your system runs smoothly. We recommend the following maintenance schedule:
- Replace the lead disc to maintain optimal performance.
- Ensure proper functionality by replacing the wire shear indicator.
- Replace the coupling to main vane stem spring pin.
- Remove the valve and the joint face gasket material and its cover. Take out the old lubricant, clean the valve, and then add new lubricant
- Inspect vanes and stems for fatigue cracks
- Check for excessive looseness in brass vane stems bearings (plain and thrust) and replace, if needed
- Inspect the main drive pinion for excessive wear. If the pinion needs to be replaced, the entire vane will also need to be replaced
- Before reassembling the actuator to the valve, check for smooth operation. It’s normal for the assembly to take slightly more effort to overcome the drag of the “O” rings
Contact Air Relief
Looking to improve your centrifugal air compressor’s energy efficiency and reduce maintenance costs? Contact Air Relief to learn more about our inlet guide vanes and how they can enhance your compressor performance.